In 2018, a pharmaceutical labeling error caused babies in Spain to be dosed with medication for hair loss. As a result, they developed hypertrichosis (werewolf syndrome) which caused them to grow thick and dense hair.
To keep the situation under control, the Spanish Health Ministry recalled batches of the medicine and closed the factory where the drug was produced.
This incident shows the grave consequences of pharmaceutical labeling errors and how they negatively impact the brand reputation and trust that consumers have placed on companies.
That’s why it’s important to tackle these errors early on to maintain the brand’s reputation and escape hefty fines and recalls.
So, in this article, we’ll look at the most common errors in pharmaceutical labeling and how to reduce these labeling errors.
Let’s start with the most common pharmaceutical errors and their causes.
Different types of pharmaceutical errors you should look out for
56 lots of asthma treatments sold in US retail outlets were recalled because they failed to include information on when the consumer should stop taking medicine and consult a doctor.
A Spanish company recalled products because it omitted the word “not”, which could put lives at risk. The product’s leaflet stated that “pseudoephedrine is excreted in breastmilk, so this product should be taken during breastfeeding” instead of “should not be taken during breastfeeding.” (Source: Schlafender Hase)
You’ll see plenty of pharmaceutical labeling errors like this with far-reaching consequences, so you’ve got to have a good understanding of the different types of errors you should be on the lookout for. Here are a few types:
- Compliance errors: These errors occur when a significant amount of regulatory information is omitted or included incorrectly in an artwork. The first incident is an example of a compliance error as it omitted compulsory regulatory information.
- Context or meaning errors: If the information on the artwork is presented incorrectly or ambiguously, it’s said to have a context or meaning error. For example, a vulnerable drug can lose potency if “store at 1-4℃” appears as “store at 14℃” due to a context error.
- Content error: Any significant error in the content that leads to potential injury or immediate death. Omitting decimal points, missing hyphenations, misspelling drug names, etc., are examples of content errors. The second recall incident mentioned above is also an example of content error.
- Technical error: This means some technical aspects of the label are missing or included incorrectly. Barcodes that are missing, incorrectly printed, or smudged are examples of technical errors.
- Readability error: These errors occur when a label’s mandatory statements aren’t conspicuous and cause readability issues which could be a source of significant medical errors. Packaging labels lacking contrast and insignificant font sizes are readability errors.
- Country-specific errors: If you’re launching your drug in different countries, you’ll have to adhere to the labeling requirements of that country or risk fines and recalls because of country-specific errors. Making translation errors, omitting translations and imagery requirements are all examples of country-specific errors.
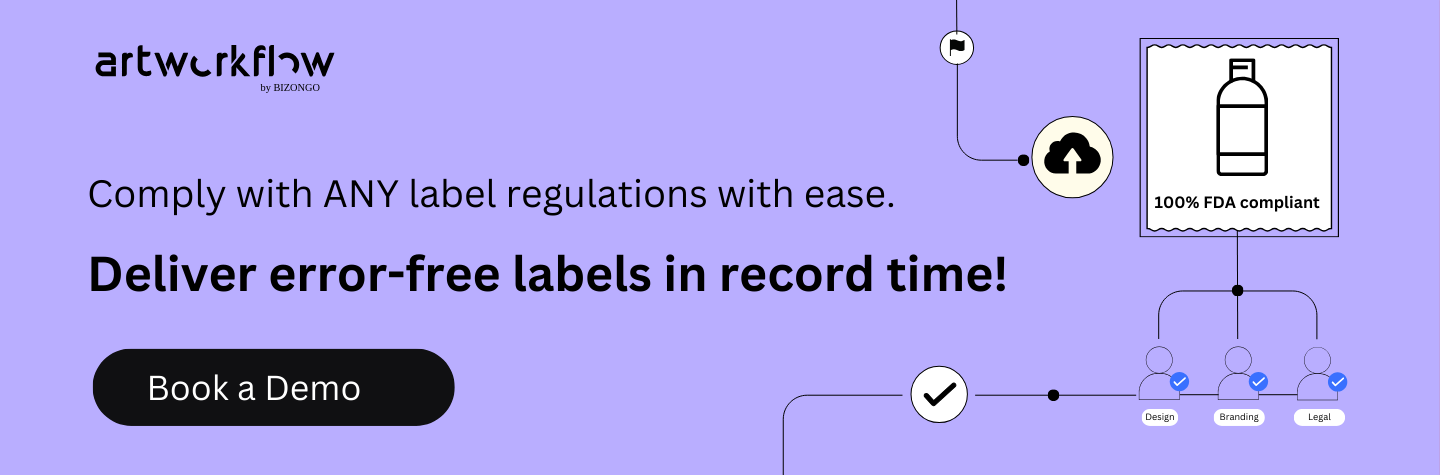
Now that we’ve looked at the different types of errors, let’s take a closer look at their implication for patients and the company.
The harmful impact of pharmaceutical errors on artwork labels
Proofreaders are “the air traffic controllers of pharmaceutical labeling and packaging. They have to get it right, because the consequences can be far-reaching,” says Dr. Jutta Hohenhoerst, Regional Sales Director, Schlafender Hase.
Dr. Hohenhoerst’s right because consumers and healthcare professionals look to the label for information and instructions on its safe and effective use. So, any error in the artwork or label contents will have far-reaching implications like:
- Adverse effects on patients: Apart from causing harm to a patient’s well-being and risking their lives, pharmaceutical errors also break the trust that patients and healthcare professionals have in the brands, as patients and healthcare staff believe that a medicine or drug will improve their health instead of negatively impacting it. As a result, you lose sales and brand equity in the market.
- Regulatory fines: The regulatory environment for pharma is becoming more stringent than ever, so even missing a hyphen, or a period can cause serious implications like class 1-A product recalls and hefty fines.
- Negative impact on internal teams: Recalls negatively impact two teams — the one handling the recall and the one involved in the artwork process. The former will have undue stress to remove the products from the supply chain quickly, and the latter will face enquiries and corrective and preventive actions. Overall, recalls affect the team morale and performance.
- Plummeting bottomline and reputation: Causing errors that negatively affect patients’ lives go against a company’s core values and will have an unfavorable impact on sales and publicity. This loss will also be compounded by the cost of recalls, lawsuits, repackaging, re-marketing, and market re-supply, which cause a dent in the bottom line.
But to avoid these errors and the harmful impacts, let’s take a closer look at the factors that cause these errors.
The most common causes of pharmaceutical errors
Most pharmaceutical errors occur due to the following reasons:
- Human limitations: Your internal team can make mistakes in the labeling process due to factors like working in a stressful environment, being constantly interrupted by other colleagues, or lacking the knowledge required to operate software or systems.
- Lack of checklists: If there are no checklists that detail what a team member should do to complete a task, it’s bound to leave room for errors. For example, if a reviewer is simply asked to review an artwork and ensure it’s compliant without any checklists, they’re bound to miss some important but minute details like expiry date, especially if they’re working on other artworks simultaneously.
- Inappropriate decision-making: Even the most competent team can make errors if the decision-making process is flawed. For instance, if management decides to adhere to an unrealistic timeline, the team members may cut corners in the labeling process, resulting in artwork labeling errors.
- Errors in information sources: If your team uses the wrong version of the source document or if the source document contains errors, reviewers will ignore them, and the labels will be printed incorrectly.
The causes mentioned above seem obvious, but you’ll be surprised at how many companies don’t pay attention to them and end up paying hefty fines and dealing with product recalls.
And the best way to eliminate these causes is to use a standard operating procedure and adhere to a lean Label design software, both of which can be easily established with an online pharma artwork management tool.
This helps the teams stay on track, reduce revisions, and finish the artwork label before the deadline. It also helps them make swift changes to artwork designs if a new regulatory requirement is introduced. So, next, let’s look at how an online artwork management tool makes the drug labeling process easier.
Why you need an online artwork management software for your drug labeling process
An online label software helps you streamline your labeling process and avoid errors which cause serious implications. Here’s how:
1. Eliminates process gaps and inconsistencies
An online artwork management tool like Artwork Flow has workflows and checklists that helps you establish an SOP and get everyone on your team on the same page regarding the whole process.
It also injects accountability and traceability into the process, so the project manager knows which team member is responsible for a specific task.
For example, with Artwork Flow, a pharmaceutical labeling project can be split into multiple stages like briefing, design, and review. And each of these stages can have tasks which the project manager can assign to different team members.
This helps locate the error sources quickly, evens out the workload distribution, and helps members understand priorities. As a result, stress-related and decision making errors are eliminated completely.
2. Automates the proofing process
You can no longer be reliant on manual proofing as your proofreaders are subject to constant stress and fatigue, especially when they’re working on multiple projects that are similar in nature.
That’s why you need an online label management software like Artwork Flow which has a set of proofing tools like the ones below to identify the different types of labeling errors.
- Spell-check tool: Eliminates content errors and ensures that they don’t tarnish your brand reputation.
- Online measurement scale: Helps you avoid compliance and readability errors and ensures that your font and imagery are the right sizes.
- Color extractor: It’s hard to identify the difference between “#03cffc” and “#00c4f0,” but any inconsistency in color paves the way for counterfeits. To prevent this from happening, you’ve got to use a color extractor tool.
3. Adhere to regulatory compliance
Regulations aren’t limited to just identifying spelling errors that can cause grave consequences. According to the FDA’s 21 CFR Part 11, companies are required to maintain an audit trail to show everyone who worked on the label and signed off on it.
And if you have an artwork management system like Artwork Flow, this process becomes a breeze.
As mentioned earlier, the workflow feature helps maintain a record of everyone who worked on the project. And the Artwork Flow library, which also doubles as a Digital Asset Management (DAM) tool, maintains a record of all the changes made to the artwork.
With the collective data from these tools, it’s easy to create an audit trail with all the tasks, the changes made to the artwork, and the members who worked on it.
Conclusion
Pharmaceutical labeling errors have far-reaching consequences that go beyond product recalls and fines.
Companies have to deal with lawsuits, backlash from the medical community and patients, and spend millions of dollars trying to rebrand their image and earn back consumers’ trust.
The best way to prevent these serious mishaps and nip these errors in the bud is to invest in an artwork management tool like Artwork Flow which has a set of proofing tools and other features which help you stay compliant.
For example, Ashish Life Sciences, manufacturers of animal health and veterinary products used Artwork Flow to eliminate labeling errors, stay on top of regulation, and improve their go-to market time.
If you want to join the bandwagon and learn how Artwork Flow can help eliminate instances of recalls and errors that cause dire consequences, get a demo right away.