Medical device labels are critical for patient and consumer safety. They serve as the primary source of information for a wide range of users, including medical professionals, patients, and consumers. Inaccurate or misleading information on a medical device label can lead to serious consequences, including confusion, misuse of the device, and even life-threatening situations.
For instance, if a label fails to provide clear instructions for use, a patient may inadvertently use the device incorrectly, potentially causing harm. Similarly, if a label doesn't adequately warn about potential risks or side effects, a patient may not be fully informed about the potential consequences of using the device.
Therefore, ensuring the accuracy and completeness of medical device labels is paramount. A well-defined pre-press SOP plays a vital role in achieving this goal by establishing a systematic review process to catch errors and inconsistencies before labels go to print.
FDA regulations for medical device labels
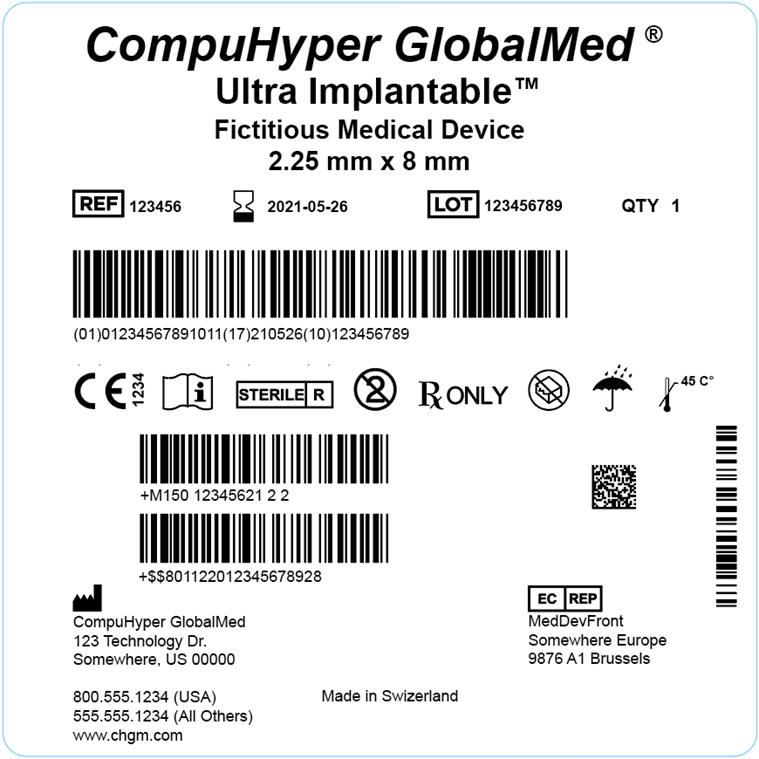
Source: Med Device Online
The US Food and Drug Administration (FDA) plays a critical role in ensuring the safety and effectiveness of medical devices. One crucial way they achieve this is through strict regulations governing medical device labels. These regulations are outlined in the Federal Food, Drug, and Cosmetic Act (FD&C Act) and enforced by the FDA's Center for Devices and Radiological Health (CDRH).
Here's a deeper dive into some key aspects of FDA regulations for medical device labels:
- Content requirements: The FDA mandates that medical device labels include specific information to ensure safe and effective use. This mandated information typically falls into the following categories:some text
- Device identification: This includes the device name, model number, and any catalog numbers for easy identification.
- Intended use: A clear and concise description of the purpose for which the device is intended.
- Instructions for use: Detailed step-by-step instructions on how to properly use the device, often accompanied by diagrams or pictograms for clarity.
- Warnings and precautions: Information highlighting potential risks, side effects, and situations where the device should not be used.
- Contraindications: A list of conditions or situations where the device should not be used due to potential harm.
- Manufacturer information: Contact details of the manufacturer, packer, or distributor for inquiries or reporting issues.
- Date of manufacture and expiration date (if applicable): This ensures users are aware of the device's shelf life and potential degradation in performance over time.
- Accuracy and completeness: The FDA demands that all information on the label is factually accurate, up to date with the latest device specifications, and sufficient to guide safe and effective use.
- Clarity and readability: The FDA emphasizes the importance of clear and concise language that is easy for the intended audience to understand. This may involve using plain language, avoiding technical jargon, and following specific guidelines for font size, color contrast, and layout to ensure optimal readability.
- Formatting and design: The FDA regulations don't dictate a specific design format for labels. However, they do emphasize consistency and clarity. This means using a well-organized layout, standardized symbols, and icons, and ensuring all elements (text, graphics, barcodes) are clear and easy to interpret.
- Labeling for different risk levels: The FDA classifies medical devices into different risk categories based on their potential for causing harm. The level of detail and stringency of labeling requirements may vary depending on the risk classification of the device. For instance, labels for high-risk devices may require more elaborate instructions and warnings compared to low-risk devices.
Things to watch out for in a pre-press review
A pre-press review is the final line of defense before a medical device label goes to print. During this critical stage, even a seemingly minor oversight can have significant consequences. Here's a breakdown of key areas to scrutinize during a pre-press review, going beyond the basics:
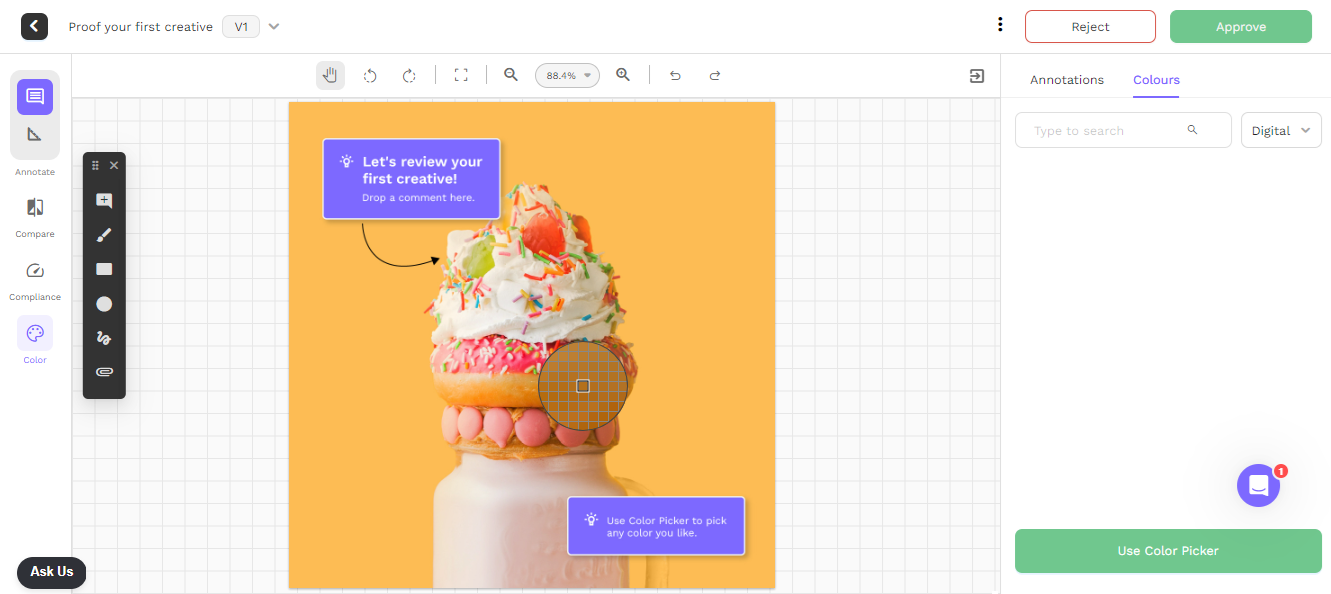
Content accuracy: a multi-layered approach
Accuracy is paramount. Verify all information against approved product specifications, but don't stop there. Here's a deeper dive:
Version control
Ensure the reviewed label is the most recent, final version, reflecting any approved changes or updates.
Unit consistency
Double-check units of measurement (e.g., milligrams vs. grams) for consistency throughout the label and alignment with intended user expectations (e.g., healthcare professionals vs. patients).
Date verification
Confirm the accuracy of the date of manufacture and, if applicable, the expiration date. Outdated labels can create confusion and compromise patient safety.
Claims and marketing language
Scrutinize any claims made on the label to ensure they are truthful, supported by scientific evidence, and don't cross the line into misleading marketing.
Regulatory compliance: beyond the basics
While adhering to core FDA labeling regulations is crucial, consider these additional steps:
Classification-specific requirements
Research any specific labeling requirements applicable to your device class (e.g., Class I, II, or III). The FDA may have additional guidance documents outlining more stringent labeling needs for higher-risk devices.
Symbol verification
Ensure all symbols used on the label, including warnings and pictograms, comply with relevant international standards (e.g., ISO) and are easily understood by the target audience.
Formatting and design: optimizing user experience
Readability and user experience are key. Here's how to ensure your label design is optimal:
Target audience consideration
Tailor the font size, complexity of language, and visual elements to the intended user. For instance, labels for patients may require larger fonts and simpler language compared to those intended for healthcare professionals.
Color accessibility
Be mindful of color blindness and ensure sufficient color contrast between text and background for optimal readability by all users.
Logical flow and white space
Organize information on the label in a logical and easy-to-follow sequence. Utilize white space effectively to avoid clutter and improve visual hierarchy.
Language: ensuring clarity across borders
For multilingual labels, a meticulous review process is essential:
Cultural nuances
Ensure translations consider cultural sensitivities and adapt terminology or imagery to resonate with the target audience.
Translation qualification
Verify the translators' qualifications and experience in medical device translation to ensure technical accuracy and adherence to relevant terminology standards.
Back-translation
Consider a back-translation process, where the translated label is translated back into the original language for a final verification of meaning and consistency.
By meticulously reviewing these aspects during a pre-press review, you can significantly reduce the risk of errors and inconsistencies on your medical device labels. Remember, a single mistake can have serious consequences, so a thorough and well-defined pre-press SOP is an essential safeguard for patient safety and regulatory compliance.
How to streamline your print inspection workflow
A well-defined pre-press SOP is the cornerstone of a robust medical device labeling process. However, its effectiveness hinges on a streamlined workflow that ensures efficiency and minimizes errors. Here's a detailed breakdown of how to optimize your print inspection process:
1. Define roles and responsibilities with precision
- Assign clear ownership: Create a responsibility assignment matrix (RAM) that explicitly outlines who is accountable for each stage of the pre-press review. This eliminates ambiguity and ensures everyone understands their tasks, preventing duplication of effort and potential delays.
- Expertise matters: Identify individuals with the requisite knowledge and experience for each stage. For instance, content accuracy review might involve personnel familiar with the specific device and its specifications, while regulatory compliance checks might necessitate expertise in relevant FDA labeling regulations.
- Empower final sign-off: Designate a qualified individual for the final sign-off. This person should possess the authority and technical expertise to approve the label for printing. This final approval serves as a critical checkpoint and ensures all requirements have been met before the label goes to production.
2. Develop detailed checklists: your pre-press roadmap
- Tailored for accuracy: Create comprehensive checklists specific to your device type and regulatory requirements. These checklists should serve as a step-by-step guide for reviewers, ensuring a thorough and consistent review process.
- Content is king: Include sections for verifying content accuracy against approved product specifications. This covers details like device name, intended use, instructions, warnings, and any specific claims made on the label.
- Regulation ready: Dedicate a section to regulatory compliance checks. Ensure the label adheres to all relevant FDA labeling regulations, including content requirements, format specifications, and language considerations.
- Formatting for clarity: Include a section for formatting and design review. This ensures proper font size, color contrast, layout consistency, and the correct use of symbols and pictograms for optimal readability.
- Multilingual considerations: If your labels are multilingual, incorporate a section specifically for language review. This verifies the accuracy of translations, ensures cultural sensitivity, and adherence to relevant medical terminology standards.
- Living document: Regularly review and update your checklists to reflect any changes in regulations, labeling requirements, or your internal procedures. This ensures your review process remains current and effective.
3. Embrace technology for a streamlined future
- Document management solutions: Utilize document management software to store and track all electronic versions of your labels. This facilitates easy retrieval of past iterations for reference and maintains a clear audit trail for regulatory purposes.
- Electronic review with eagle eyes: Explore electronic review tools with comparison features. These tools can highlight discrepancies between different label versions, streamlining the review process and minimizing the risk of errors. Imagine side-by-side comparisons of content or formatting changes, saving reviewers valuable time and ensuring consistency.
- Digital proofing for real-time collaboration: Consider digital proofing systems that enable real-time collaboration and online sign-off. This allows for instantaneous feedback between internal and external stakeholders, expediting the approval process. Imagine reviewers from different locations providing comments and edits on the same digital label, all in real time.
4. Standardize communication for seamless collaboration
- Clear channels for clear communication: Establish clear communication protocols for reporting and resolving discrepancies identified during the review process. This might involve designating a specific communication channel (e.g., email thread, internal chat platform) or implementing a standardized reporting form to ensure consistent documentation of any issues.
- Timely resolutions: Define a timely response mechanism to address any concerns raised during the review. This ensures that identified issues are addressed promptly and don't cause delays in the approval process.
- Open dialogue is key: Encourage open communication and collaboration between reviewers and stakeholders. This fosters a culture of shared responsibility and ensures all concerns are addressed before final approval. By openly discussing any potential issues, mistakes can be identified and rectified before the label goes to print.
5. Leverage intelligent creative compliance solutions.
Artwork Flow provides a centralized platform for managing the entire label creation, review, and approval process. Here's how it can specifically benefit your medical device label pre-press review:
- AI-powered compliance checks: With ComplyAI, Artwork Flow integrates artificial intelligence (AI) to help you automate compliance checks against relevant FDA regulations. The AI can scan your label for missing information, inconsistencies with format requirements, and potential regulatory violations, flagging any issues for reviewers. This not only saves reviewers valuable time but also increases the accuracy and consistency of compliance checks.
- Streamlined collaboration and version control: Artwork Flow provides a central repository for all label versions, facilitating real-time collaboration between internal and external stakeholders. Reviewers can easily access different iterations of the label, add comments and annotations, and track changes made throughout the review process. This eliminates confusion over the most current version and ensures everyone is working on the same document.
- Automated workflows and pre-flight checks: These platforms can automate repetitive tasks such as version control, routing labels for review based on pre-defined workflows, and performing pre-flight checks to ensure all necessary information and files are present before sending the label to print. This minimizes human error and streamlines the entire pre-press review process.
- Improved communication and audit trails: The software often provides built-in communication tools that facilitate clear communication between reviewers and stakeholders. This allows for real-time discussions regarding discrepancies and streamlines issue resolution. Additionally, all actions taken within the platform are automatically logged, creating a detailed audit trail for compliance purposes.
Conclusion
By leveraging Artwork Flow’s ComplyAI alongside your well-defined SOP and streamlined workflow, you can achieve a new level of efficiency and accuracy in your pre-press review process. This not only minimizes the risk of errors but also frees up valuable resources for your team, allowing them to focus on more strategic tasks. Try out the demo today!