A product recall news is certainly alarming to you and your consumers. Why?
A single misstep in your supply chain can lead to a full-blown public relations crisis, leaving shelves empty and your brand reputation tarnished.
As for your consumers, a defective product can potentially affect their health which can have a long-lasting effect on them.
A product recall can also occur when your product is non-compliant with regulatory heads like the Food and Drug Administration (FDA), European Medicines Agency (EMA), Occupational Safety and Health Administration (OSHA), and more.
Apart from that, there are so many aspects you have to see to save your product from the nasty recalls. Here, we’ll explore different classifications, reasons, and consequences of product recalls and how to prevent them. Let’s make sure your next product is flawless with this survival guide!
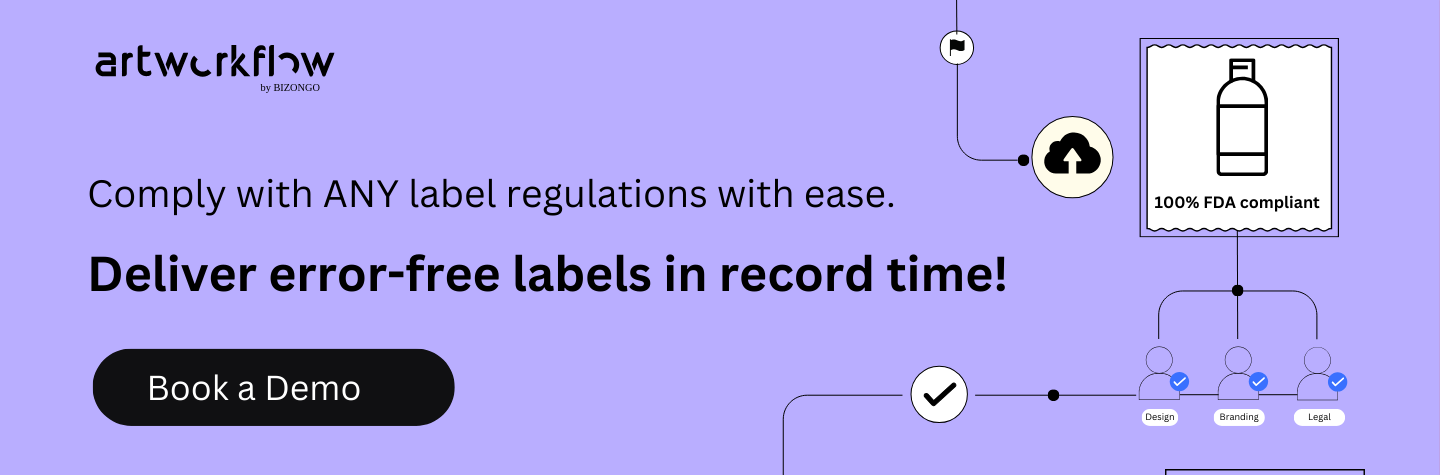
Classification of product recalls
All recalls do not pose a risk to consumers. There are products that their companies retain due to minor labeling defects. Recalls can be classified into two or three tiers based on which government agency is responsible.
Two tiers: It includes agencies overseeing products related to transportation safety, particularly road vehicles and aircraft. The National Highway Traffic Safety Administration (NHTSA) and the Federal Aviation Administration (FAA) control the products under this category.
Three tiers: Three-tier systems include agencies that regulate consumer goods that don’t include vehicles. Agencies such as the Food and Drug Administration (FDA), Food Safety and Inspection Service (FSIS), and Consumer Product Safety Commission (CPSC) control this. Let’s learn more about this classification system.
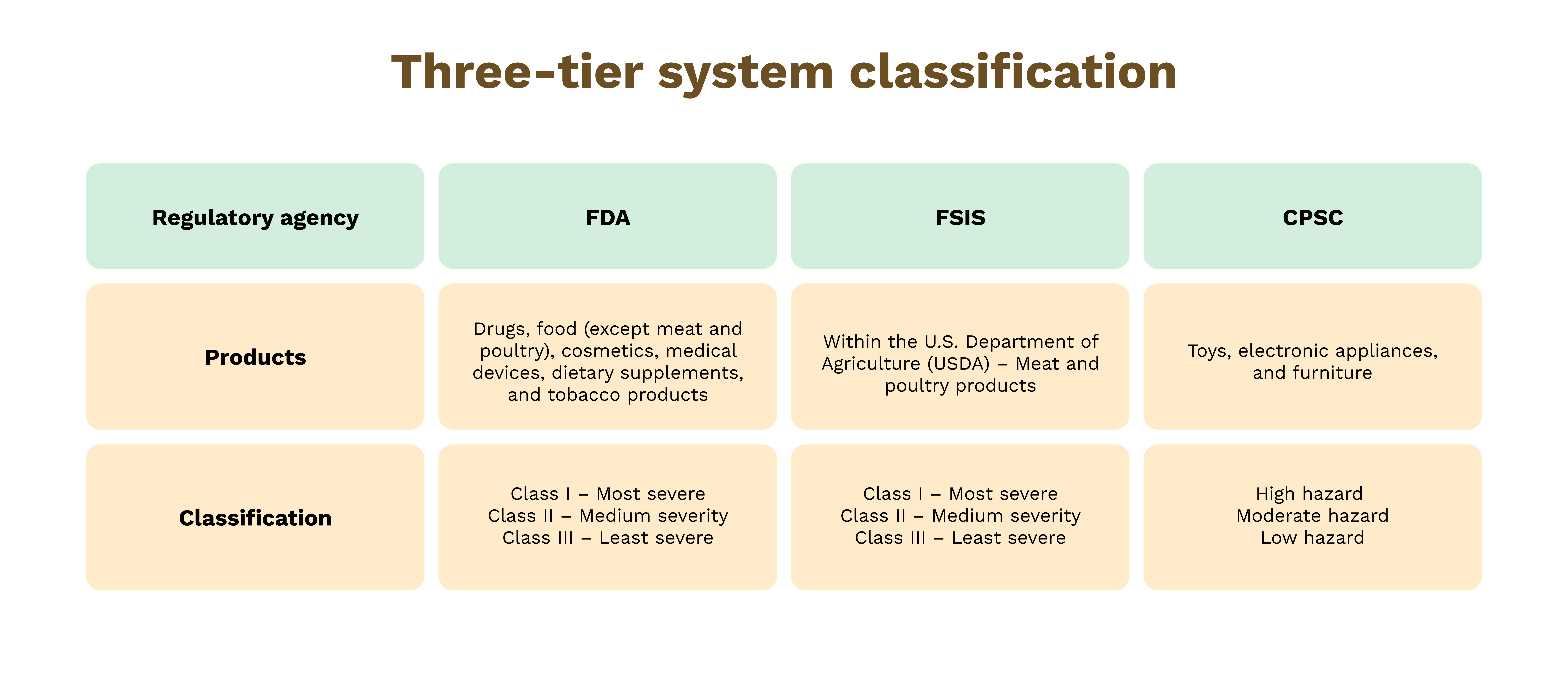
Class I: High hazard recalls
These recalls are for problematic products that can lead to serious injury or death. The result will be the products being returned or disposed of and the manufacturer issuing a refund or replacement.
E.g., Salmonella contamination in ready-to-eat food or the wrong active ingredient in drugs with serious consequences.
Class II: Moderate hazard recalls
These products can cause temporary or moderate injuries or illness.
E.g., Medication with an incorrect dosage or presence of metal in packaged food.
Class III: Low hazard recalls
These are products that are unlikely to cause harm but violate labeling or safety standards.
E.g., Faulty packaging of toys that don’t injure children or the wrong batch number of the product.
Reasons behind a product recall
Product recalls can be triggered by a variety of issues, some arising at the production stage, and others identified later. Here are the top reasons products are withdrawn from the shelves of stores or households:
1. Manufacturing defects
This is when blunders occur during production, creating a physical defect in the product. Imagine a children's toy with a piece that can easily break off, posing a choking hazard, or an overheated hair straightener producing harmful chemicals. Manufacturing defects can compromise the product's functionality, durability, or safety.
2. Inaccurate labeling
Misleading or incorrect information on labels can be unsafe. For instance, food labels might not list all ingredients, putting people with allergies at risk. Inaccurate labels can also create confusion about usage instructions, potentially leading to misuse of the product.
3. Non-compliance with mandatory standards
Every industry has safety regulations products must meet. If a product fails to meet these standards, a recall might be necessary.
For example, MoCRA's recent labeling regulations require manufacturers to include their domestic contact information within the US if adverse events occur. If this is not implemented within the given time frame, the cosmetics company will find itself in the news for being a non-compliant product.
Also read: A Makeover for your Cosmetic Brand: What You Need To Know About MoCRA
4. Undeclared ingredients
This can happen unintentionally, due to errors in the supply chain, or even in negligence. Undeclared ingredients can trigger allergic reactions or other health problems for consumers with sensitivities. Food products are especially prone to this type of recall.
Also read: Everything You Need to Know About Food Allergen Labeling In 2024
For instance, DSD Merchandisers, LLC, in cooperation with the FDA, recalled its Deluxe Roasted & Salted Mixed Nuts due to undeclared peanuts. This was thanks to the investigation they did upon a consumer’s feedback which helped the company take proper action on time. Recalls initiated by manufacturers themselves are called voluntary recalls.
5. Presence of bacteria and foreign materials
Contamination of products with harmful bacteria can occur at various stages, from manufacturing to storage. It mainly causes foodborne illnesses, so recalls are crucial to prevent outbreaks. Some bacteria the FDA has listed in the U.S. to watch out for are salmonella, listeria, e.coli, and norovirus which can hospitalize or even cause the death of the consumer.
The presence of unexpected objects such as plastic pieces, metal particles, or even counterfeit drugs embedded in a product can pose a choking hazard or cause a serious health threat. It is also a result of malfunctioning in quality control during the manufacturing process. In 2023, top soft drink brands like Diet Coke, Sprite, and Fanta were recalled by the FDA due to ‘potential foreign material’. It is a reminder that this can happen to any brand.
6. Scattered supply chain management
It is likely that a low-quality product will be produced if a company's supply chain management fails to have smooth collaboration between teams or is inadequate in monitoring a complex supply chain process. One such example is the recall of the cinnamon-flavored applesauce pouches by Schnuck Market Inc. due to the presence of a high level of lead in their products. This was informed to the company by the supplier, Purcell International, who found the lead in the cinnamon raw material used by Austrofood SAS, the manufacturer of the applesauce cinnamon pouches. An adequate communication and quality control system could have avoided the situation here.
7. New product model with no safety history
Brand new products haven't had the benefit of extensive real-world use and testing. If a potential safety concern arises, a recall might be issued as a precaution until more data is gathered. This ensures potential problems are caught early on.
How much does a recall cost and what are its other consequences?
Product recalls are essential for protecting consumers from damage but they come at a steep price for manufacturers. The National Center for Food Safety & Toxicology report states that product recalls cost the U.S. economy an estimated $100 billion annually. While the financial losses can be staggering, the true cost lies in the potential harm to consumers, the damage to brand reputation, and the legal and regulatory challenges that follow.
Financial crisis
The financial burden incurred from the product recall is unpredictable. You have to cover several unexpected costs for product retrieval, replacement, and disposal. Some of the costs include:
- Informing the respective regulators.
- Reorganizing the entire supply chain.
- The retrieval of the product by store or geographical location.
- Storage of sets of recalled products.
- Testing out the recalled product to find the source of the cause.
- Loss of product that didn’t go for sale.
Depending on the severity of the issue, repairs or refunds for affected consumers may be necessary. Additionally, investigations and potential lawsuits can further drain company coffers.
Consumer risks
The most critical impact is the potential risk to consumer safety. Defective or non-compliant products can cause permanent injuries or illnesses to your customers. Recalls mitigate these risks but the damage can already be done for consumers who have already used the product.
Damaged reputation
Product recalls can severely degrade a company's reputation. Unwanted media attention, consumer distrust, and loss of brand loyalty can take a long time to recover from. Building trust takes years, but losing it can happen overnight with a single high-profile recall.
Legal issues
Lawsuits are a frequent result of product recalls. Consumers who have been injured or suffered damages can sue the manufacturer, leading to hefty settlements or court battles. The legal fees associated with defending these lawsuits can add another layer of financial burden.
Regulatory liabilities
Regulatory bodies will investigate the cause of the recall and may impose fines or penalties depending on the severity of the recall. These fines can be big and the particular company may face stricter oversight in the future, affecting production processes and increasing compliance costs.
Best practices to avoid recalls
While it is easy to be a victim of product recalls, it is not easy to stop them. What you can do is prioritize quality control and have preventive measures including a full recall plan in place. Here are some actionable tips to steer clear of product recalls.
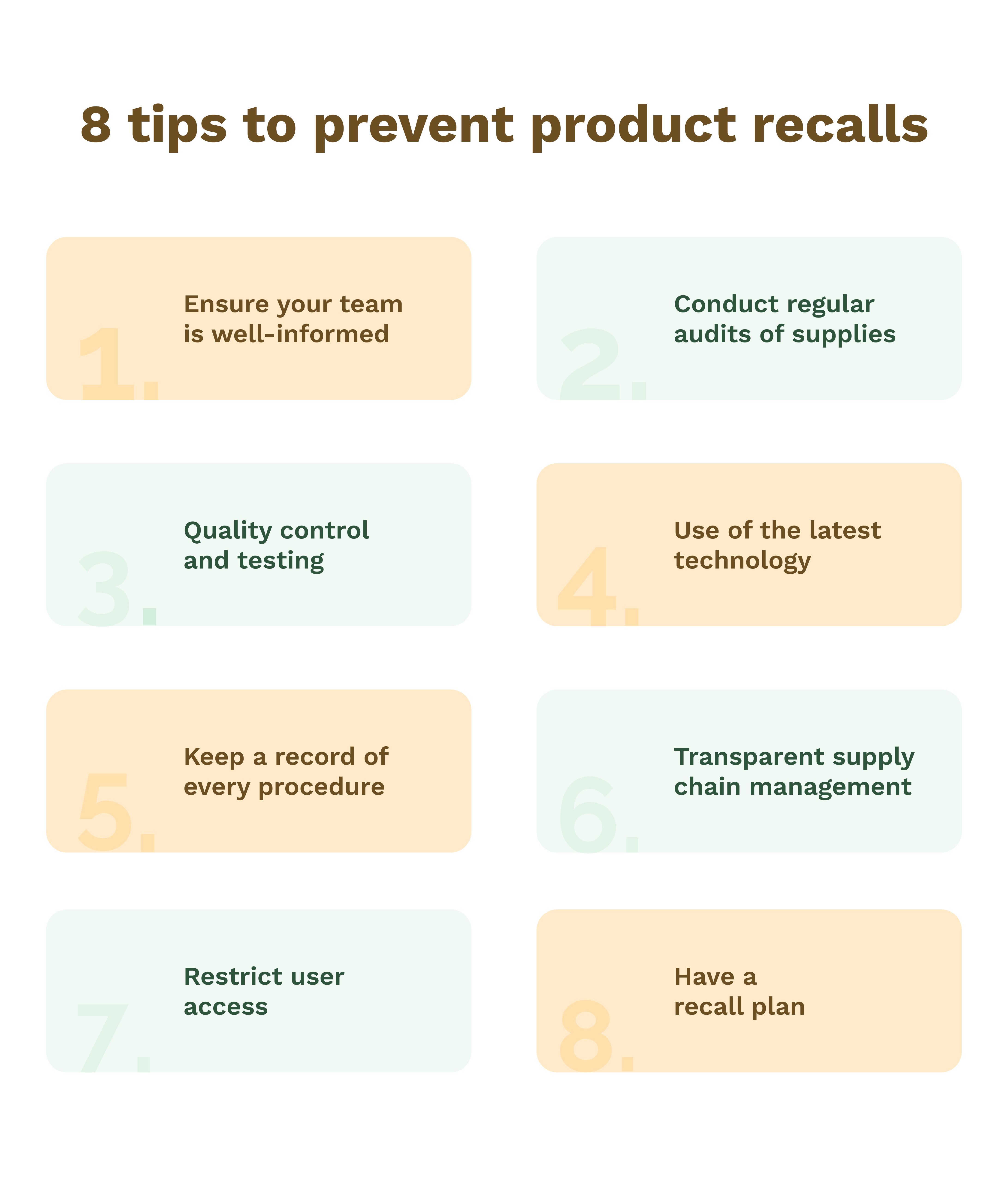
Keep your team in the loop
- Practice open communication to remain transparent during the whole product development and manufacturing process. Encourage your employees to report any concerns they might have about materials, processes, or finished products.
- Hold regular training sessions to brief employees on updated industry regulations, safety protocols, and potential hazards.
Maintain regular audits of raw ingredients
- Partner with reliable suppliers who prioritize quality control, and sign a contract with them to hold them accountable for the activities.
- Schedule regular audits of raw materials and components.
- Keep detailed records of audit dates, suppliers' certifications, and their past performance.
Quality control and testing
- Have an expert team dedicated to overseeing the quality control systems.
- Implement rigorous quality control measures throughout the production process. This includes random inspections, testing of finished products, and maintaining detailed records.
- Remember to study and test your product at each vital point to ensure it’s coming well and working fine.
Integration of AI and technology
- How could we keep up with the recurring product demands if it weren’t for latest technology? Integrate AI-powered tools into your quality control processes.
- Use the best tools to analyze data, identify potential problems early, and predict areas where issues might arise.
- You can also integrate smart label compliance software like ComplyAI to launch the perfect packaging labels in the market.
Learn more about ComplyAI and how it helps with certain compliance requirements.
Document every procedure
- Maintain documentation of every single procedure meticulously, from initial design to final production.
- This creates a clear audit trail that helps troubleshoot and identify the root cause of any issues that might arise.
Efficient supply chain management
- Establish a clear communication route between suppliers and other stakeholders with supply chain management software and cloud-based platforms.
- Improving supply chain visibility helps you locate affected products quickly so they can be removed from the distribution network. Technologies like blockchain can create a clear and secure record of how products move.
Define user control and access points
- Set user control within your product’s design and functionality.
- For employees and clients include areas that are particularly vulnerable to tampering such as mixing, or ingredient preparation.
Have a recall plan in place
- Within the team, design detailed recall plans that outline roles, responsibilities, and communication protocols during the product withdrawal.
- Define product retrieval procedures and establish protocols for customer support.
Bonus tip: Install a customer support portal to encourage your customers to report a problem with the product. In this way, you can investigate and resolve the issue in advance rather than having to deal with it after the market retracts your product.
Prevent recalls with Artwork Flow’s ComplyAI
In the era of AI and a fast-paced market, keeping up with competition is crucial. It is common to make errors with your labels in such situations. That’s where a smart label compliance feature like ComplyAI becomes your Hawkeye. It ensures your product is safe by helping you automate compliance in specific areas.
How does ComplyAI work?
Dealing with numerous products at the same time can be risky and confusing. Especially when you have to keep up with the changing rules and restrictions occasionally.
ComplyAI helps you stay compliant, regardless of the breadth and diversity of your product line. Here, you get to create and customize rulebooks for various packaging label projects where you can proof artwork for:
- Text (i.e., information such as brand name, nutritional values, and disclaimers).
- Images (i.e., logos and warning symbols).
- Grammar and font size requirements.
Additionally, to define more specific rules on the elements mentioned above, there are conditional rules where, if the first rule you set is met in the results, then ComplyAI can automatically check for a second rule during the same check, letting you work more efficiently.
For example, if ‘Drug Facts’ is found on the artwork, it must be in the font Helvetica Bold Italic with a size of 9 pt.
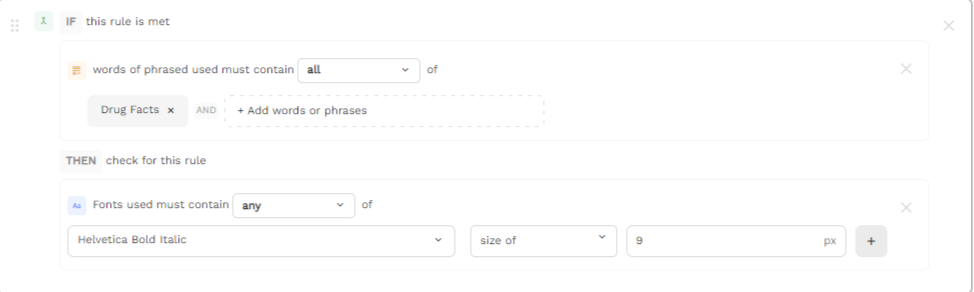
Now, let’s see how ComplyAI can help maintain compliance with regulations and prevent costly recalls.
- Automated compliance for label regulations: Stay updated with your product labels and steer clear of regulatory issues by running label compliance checks backed by AI with the latest guidelines by the FDA, EU, FSSAI, and more.
- AI-powered proofing: ComplyAI scans your artwork for even the most minor discrepancies. This includes misprints, typos, grammar, and missing information on labels. Catching these errors early prevents the production and distribution of potentially non-compliant products.
- Allergen alert: Undeclared allergens are a major cause of product recalls. They accounted for 49% of recalls in 2023, a 27% increase over 2022. ComplyAI engine flags any missing allergen information on labels, ensuring your consumer’s safety and avoiding costly recalls.
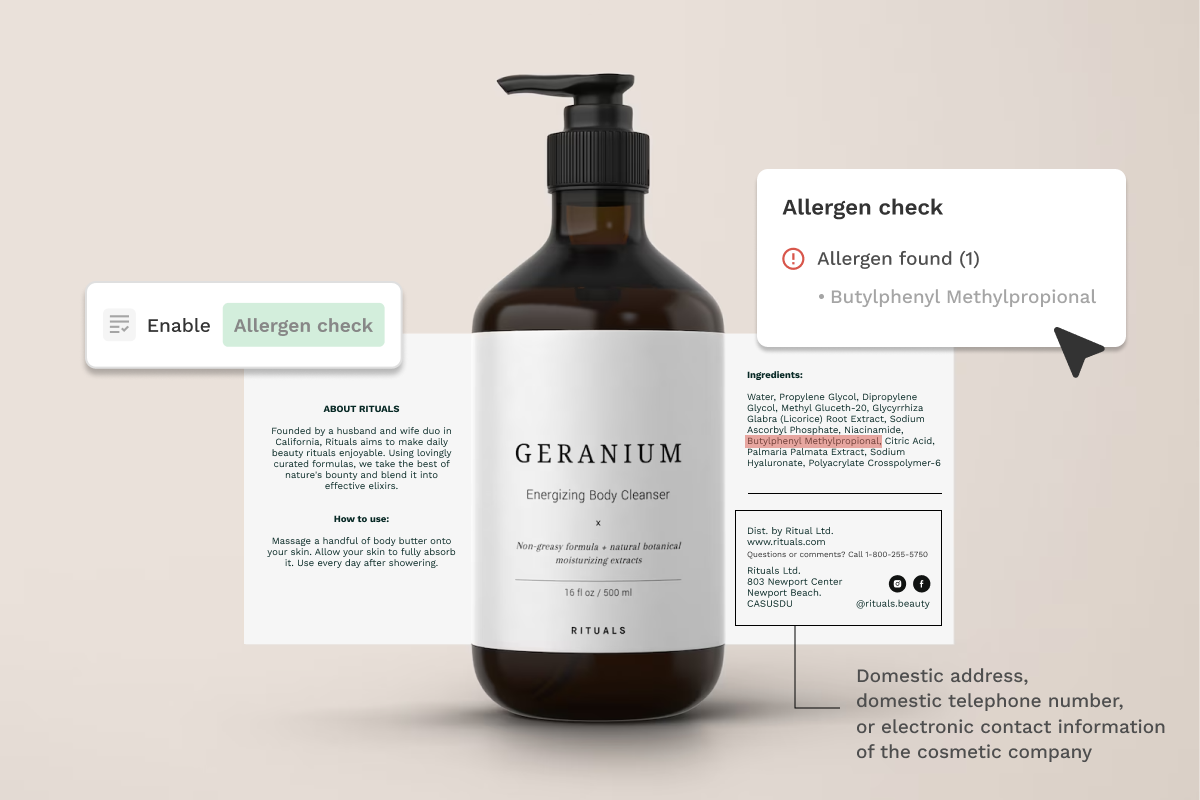
- Barcode scanner: A barcode is important for disseminating product information. If the information is incorrect or the barcode is invalid, there is a risk of product recalls. It can also disrupt the supply chain and create confusion.
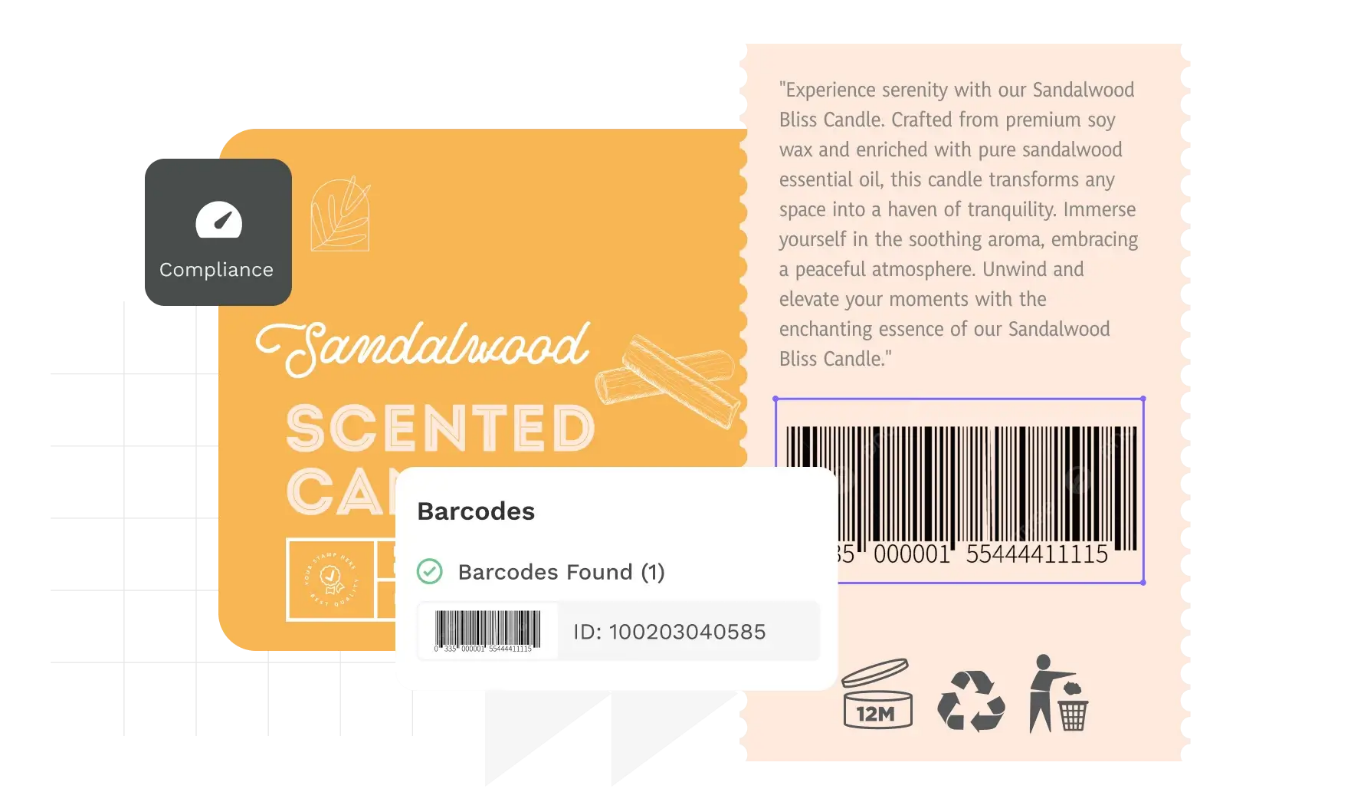
By automating tedious manual review and verification tasks, ComplyAI frees up your team to focus on other critical areas. This increases efficiency and reduces stress, allowing you to focus on what matters most — creating high-quality and safe products.
Note: ComplyAI is a label compliance software that does not in any way offer recommendations. To learn more about any regulation, head to its respective site for more information.
Conclusion
By proactively preventing errors, you can ensure your products are safe, compliant, and meet consumer expectations. For that, consider the best options out there such as choosing the best manufacturer or adopting software that helps you collaborate transparently with your team members to launch compliant products.
ComplyAI by Artwork Flow is an investment in simplifying your label compliance tasks. Whether you’re in food and beverages, cosmetics, pharma, or chemicals, ComplyAI can run automated and regulatory compliance checks with ease.
Artwork Flow, as a label management platform, offers you an all-in-one solution such as label review, smart proofing, print inspection, version control, and more. You can schedule a demo with our experts to learn more.